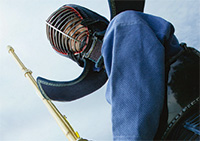
Today we are recognised as the world’s premium maker of specialist indigo dyed cloth used in the making of the traditional uniform for practitioners of kendo. With this history, experience and technical expertise in our arsenal we are moving into the modern world with our collection of contemporary apparel and interior accessories at the same time as exploring opportunities to expand into international markets.
Opening greetings
During the 140 plus years since our company’s foundation, we have concerned ourselves with nurturing traditional techniques in indigo dyeing whilst incorporating the latest technological manufacturing developments. At the same time we are working hard to further develop different techniques and to deepen our technical know-how in order to maximise the benefits of natural indigo. As a result we have the utmost confidence in our ability to create appealing products that meet the demands of the most discerning consumer and take the centuries old tradition of indigo dyeing into the next generation.
As a company Kojima Senshoku has always been ahead of its time in terms of our keen awareness of environmental issues. We operate our own large-scale drainage system and conserve water 24 hours a day, 365 days a year according to very strict regulations. In addition to this we make regular donations to groups concerned with protecting the natural environment and run activities and events ourselves to raise awareness of the importance of water conservation. We also prioritise techniques and processes that can be carried out manually and do not rely on machinery or require natural resources to power them.
At Kojima Senshoku we believe that the wealth and abundance with which we are surrounded in the modern age of materialism is not divorced from Nature but intricately interlinked with and dependent upon it. In this way, we aim to create indigo dyed products that reflect the abundance and beauty of the natural world.
History and the present
Kojima Senshoku was founded in 1872 by Kumahei Kojima. The main focus of the business at that time was the manufacture of workwear for farmers. This was because indigo has been known since ancient times as having effective natural insect repellent qualities.
Now our main business lies in the manufacture of specialist kendo uniform and traditional clothes worn at festivals. Devotees of indigo value the durability and stiffness of the cloth as well as the fact that, the more the cloth is worn, the more nuanced and characterful it becomes.
The secret of the charm of Kojima Senshoku cloth lies in the fact that we take our time and tolerate no compromises. We have mastered techniques that enable us to produce on a large scale without making any sacrifice in terms of quality. Using time honoured techniques and expertise combined with modern technological innovation we are able to create pieces in traditional indigo dyed cloth that surprise and inspire.
Introduction to the manufacturing process
Let me explain about the manufacturing process.
The 1st process is called “kase-age”. At Kojima Senshoku we use a traditional form of kase-age and the first step is the take the thread from the reel and use it to form “kase”, or rope-like, looped shapes.
Next is the “ito hataki”process. This is carried out to avoid trouble further down the line when the yarn is likely to snag. The threads are arranged into a neat pattern much like a twill weave.
The next step is the actual dyeing, or “ito-zome”. The yarn, in the loop shapes known as “kase” is dipped time and time again into the indigo dye. The colour forms as the cotton is exposed to oxygen in the surrounding air. The depth of the colour depends on how many times the cotton is dipped but in most cases dipping takes place between 15 and 20 times, in repetitions of exactly the same process.
The next step is called “nori-tsuke”. Dyed thread is washed in water and then a starchy glue is applied to make it slippery and smooth.
Then thread is dried in the sun. In order to achieve the desired depth and beauty of colour the thread needs to be dried slowly under natural sunlight.
We then perform a process we call “cheese up”, taking the loops of yarn and re-forming the reel shapes they were in at the start.
Next is the warping stage. The thread is arranged using a delicate technique in order to form the warp thread for weaving.
Finally, the thread is woven on a shuttle loom. At Kojima Senshoku we still use the same shuttle looms we have used for the last 40 years. The machines demand diligent care and considerable strength on behalf of the operator.
The movement of these old machines is a sight to behold. Just watching and listening to them is in itself quite something.

Introduction to the fabric
At Kojima Senshoku we have a wide range of different traditional woven textiles.
As we use the “kase” dyeing process the dye penetrates to the very centre of the thread. Furthermore, as we use shuttle looms the resulting woven textile is of an very high thread count and is extremely dense and durable.
We have a wide selection of textiles in our collection from lightweight fabric suitable for shirts and other apparel to heavier, dense fabrics that are ideal for making bags.
Additionally, as suppliers of fabric for martial arts uniforms, most notably for practitioners of kendo, we are known for our “sashiko” or thick, durable quilted cloth. We have a wide range of sashiko cloth available, from the “saki-zome” (yarn-dyed) to double-weave, “ato-zome” (piece-dyed) and so on. We also sell the “kase-zome” yarn itself.
At Kojima Senshoku we posesss a large amount of equipment and machinery necessary for yarn dyeing, piece dying and finishing. We are able to apply many different types of wash finishing, water-resistance treatments and so on according to specific requirements. In this way the same fabric can end up having an entirely different appearance, touch and functionality depending on the treatments it has undergone.
We are also working hard at developing our own range of products that showcase the beautiful characteristics of the “kase-zome” technique including “yatara koushi” (fabric woven into a random lattice pattern) and gradation dyed fabrics.
Closing words
The city of Hanyu in Saitama, facing the wide River Tone and with a plentiful supply of water, is an idyllic, pastoral satellite garden city in the outer suburbs of Tokyo. Also known as “Bushu”, the area has for over 200 years been renowned for its indigo dyeing industry, known as Bushu Indigo Dyeing, and continues to be a centre of traditional Japanese crafts.
Our factory is a haven of multi-sensory delights for people interested in arts and crafts. Visitors to the factory come up close and personal with craft in action through the smell of the indigo, the sound of the shuttles, the lurch back and forth of the sun-dried thread, the sight of the masterful craftsmen at work.
Welcome to Hanyu!
Come and see for yourself what we create up here in Hanyu. The Kojima Senshoku team look forward to extending you the warmest welcome.